Opening the Power of Welding WPS: Approaches for Efficiency and Safety And Security in Fabrication
In the world of manufacture, Welding Procedure Specs (WPS) stand as the backbone of welding procedures, dictating the essential steps for achieving both performance and safety in the manufacture procedure. Comprehending the intricacies of WPS is extremely important to harnessing its complete potential, yet several companies struggle to open real power that exists within these documents (welding WPS). By diving right into the techniques that maximize welding WPS, a world of enhanced efficiency and enhanced safety waits for those going to discover the nuances of this vital element of fabrication

Relevance of Welding WPS
The value of Welding Procedure Requirements (WPS) in the manufacture sector can not be overemphasized. WPS work as an essential roadmap that details the necessary actions to make certain welds are performed constantly and correctly. By defining important criteria such as welding procedures, products, joint designs, preheat temperatures, interpass temperature levels, filler steels, and post-weld warm treatment requirements, WPS supply a standard technique to welding that improves effectiveness, top quality, and safety in construction processes.
Adherence to WPS assists in accomplishing harmony in weld quality, decreasing the probability of issues or structural failures. This standardization also helps with conformity with industry regulations and codes, making certain that produced frameworks fulfill the required safety and security criteria. Moreover, WPS documents makes it possible for welders to replicate successful welding procedures, leading to consistent results across different projects.
Essentially, the meticulous development and strict adherence to Welding Procedure Requirements are paramount for upholding the stability of welded frameworks, safeguarding versus possible risks, and supporting the online reputation of manufacture firms for providing top notch product or services.
Key Elements of Welding WPS

Enhancing Effectiveness With WPS
When maximizing welding procedures, leveraging the vital components laid out in Welding Treatment Specs (WPS) ends up being necessary for streamlining processes and optimizing productivity. One way to improve efficiency with WPS is by very carefully selecting the proper welding specifications.
Regularly reviewing and upgrading the WPS to integrate any type of lessons discovered or technological advancements can additionally add to effectiveness renovations in welding procedures. By accepting the standards established forth in the WPS and continuously looking for ways to maximize procedures, makers can accomplish higher efficiency levels and exceptional end results.
Ensuring Security in Fabrication
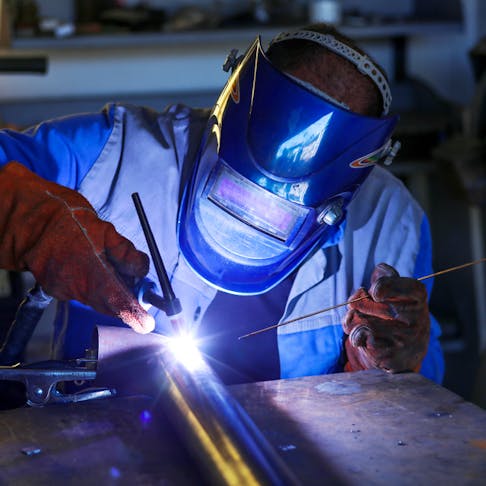
Ensuring safety and security in construction entails a diverse technique that incorporates numerous aspects of the welding procedure. Welders need to be geared up with suitable gear such as helmets, gloves, and protective garments to mitigate threats associated with welding tasks.
Moreover, adherence to appropriate air flow and fume extraction systems is crucial in maintaining a healthy workplace. Welding fumes include harmful materials that, if inhaled, can pose severe wellness risks. Implementing efficient ventilation actions assists to reduce exposure to these unsafe fumes, promoting respiratory system health and wellness amongst employees.
Normal tools maintenance and examinations are likewise vital for guaranteeing safety and security in fabrication. Damaged machinery can bring about injuries and here accidents, underscoring the significance of timely fixings and routine checks. By focusing on precaution and promoting a culture of understanding, construction facilities can develop a protected and effective workplace for their employees.
Carrying Out WPS Best Practices
To improve functional efficiency and guarantee top quality end results in manufacture procedures, including Welding Treatment Specification (WPS) best techniques is critical - welding WPS. Applying WPS finest practices entails careful preparation, adherence to market requirements, and continual monitoring to ensure optimal results. First of all, choosing the appropriate welding process, filler material, and preheat temperature defined in the WPS is essential for achieving the preferred weld quality. Secondly, making certain that qualified welders with the necessary certifications execute the welding treatments according to the WPS guidelines is essential for uniformity and reliability. On a regular basis examining and upgrading WPS papers to reflect any process enhancements or adjustments in materials is also a key ideal practice to keep accuracy and significance. Furthermore, offering comprehensive training to welding personnel on WPS needs and ideal methods promotes a culture of safety and security visit their website and quality within the manufacture setting. By vigilantly executing WPS finest methods, producers can simplify their procedures, reduce mistakes, and deliver remarkable items to meet customer expectations.
Verdict
Finally, welding WPS plays a critical role in guaranteeing efficiency and safety and security in construction processes. By concentrating on crucial elements, boosting efficiency, and carrying out ideal techniques, firms can maximize their welding procedures. It is vital to prioritize safety and security actions to stop accidents and make certain a smooth production procedure. By complying with these strategies, businesses can open the complete capacity of welding WPS in their manufacture procedures.
In the world of fabrication, Welding Procedure Specifications (WPS) stand as the backbone of welding operations, dictating the required steps for accomplishing both effectiveness and safety and security in the manufacture procedure. By defining necessary parameters such as welding procedures, products, joint designs, preheat temperature levels, interpass temperature levels, filler metals, and post-weld warm treatment demands, WPS offer a standardized method to welding that improves efficiency, top quality, and security in fabrication procedures.
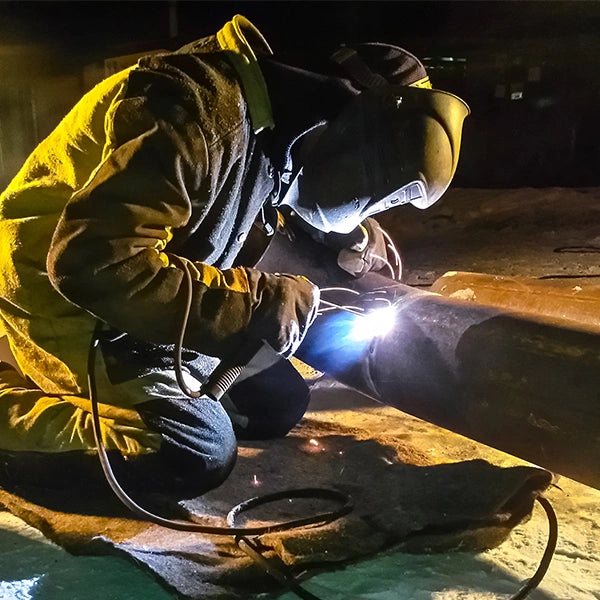
When maximizing welding procedures, leveraging the crucial elements laid out in Welding Procedure Specs (WPS) ends up being crucial for improving processes and maximizing productivity. (welding WPS)